Quality Assurance: Factory QC vs. Third-Party QC vs. Our Approach at World Sourcing
In the world of manufacturing, quality control (QC) is critical to ensuring that products meet high standards. Factory QC is often the first line of defense, but it can sometimes fall short due to internal pressures or a lack of specialized expertise. Third-party QC, commonly employed by buyers, typically conducts inspections during production in China and reports back from a different time zone, creating a time lag. This process can cause delays, as communication between the buyer and the factory often takes longer than necessary.
At World Sourcing, we take a proactive, hands-on QC approach by sending our internal QC specialists directly to the factory. We resolve any issues immediately and provide the buyer with a fix plan or results within the same business day. This enables quick decision-making, allowing us to implement adjustments and return to the factory the next day for immediate action. By ensuring quick feedback loops, we minimize delays, improve product quality, and keep the production timeline on track.
A recent case we handled highlighted the risks of relying solely on third-party QC, where defects arose due to gaps in the inspection process. By providing real-time QC and rapid communication, we ensure products meet the required standards before they reach the buyer, preventing costly defects and streamlining the entire process.
Our hands-on, real-time QC approach means fewer defects, faster resolutions, and a more efficient process. This not only helps to deliver higher-quality products but also strengthens our client relationships by providing consistent, reliable results. At World Sourcing, we’re dedicated to reducing lead times, improving product quality, and fostering transparent communication between buyers and factories.
Why Choose World Sourcing for Quality Control?
- Hands-on QC specialists directly at the factory
- Instant feedback and action within the same business day
- Minimized delays with quick communication between buyer and factory
- Prevention of defects before products reach the buyer
- Proactive approach that improves product quality and production efficiency
With our expert QC process, World Sourcing ensures that your products meet the highest standards—saving you time, reducing costs, and boosting customer satisfaction.
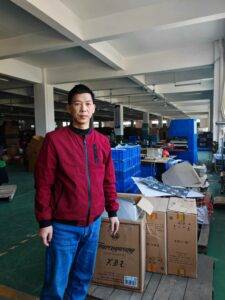
Joe Liang serves as the Quality Control (QC) Manager, bringing over 20 years of experience in the fields of Quality Assurance and Inspection. His extensive knowledge base encompasses various aspects of quality control as well as the characteristics of diverse materials and products. Throughout his career, he has engaged with a wide range of product categories, including electronics, non-electronics, hardlines, arts and crafts, and textiles, effectively covering almost all consumer items typically found in retail stores.
In his role, Joe collaborates closely with engineering and OEM teams to establish standardized protocols in the early stages of product development. This collaboration is essential for maintaining control throughout each manufacturing process. The objective is to achieve or surpass the acceptable defect rates for each product manufactured within our factory, thereby minimizing post-sale returns.